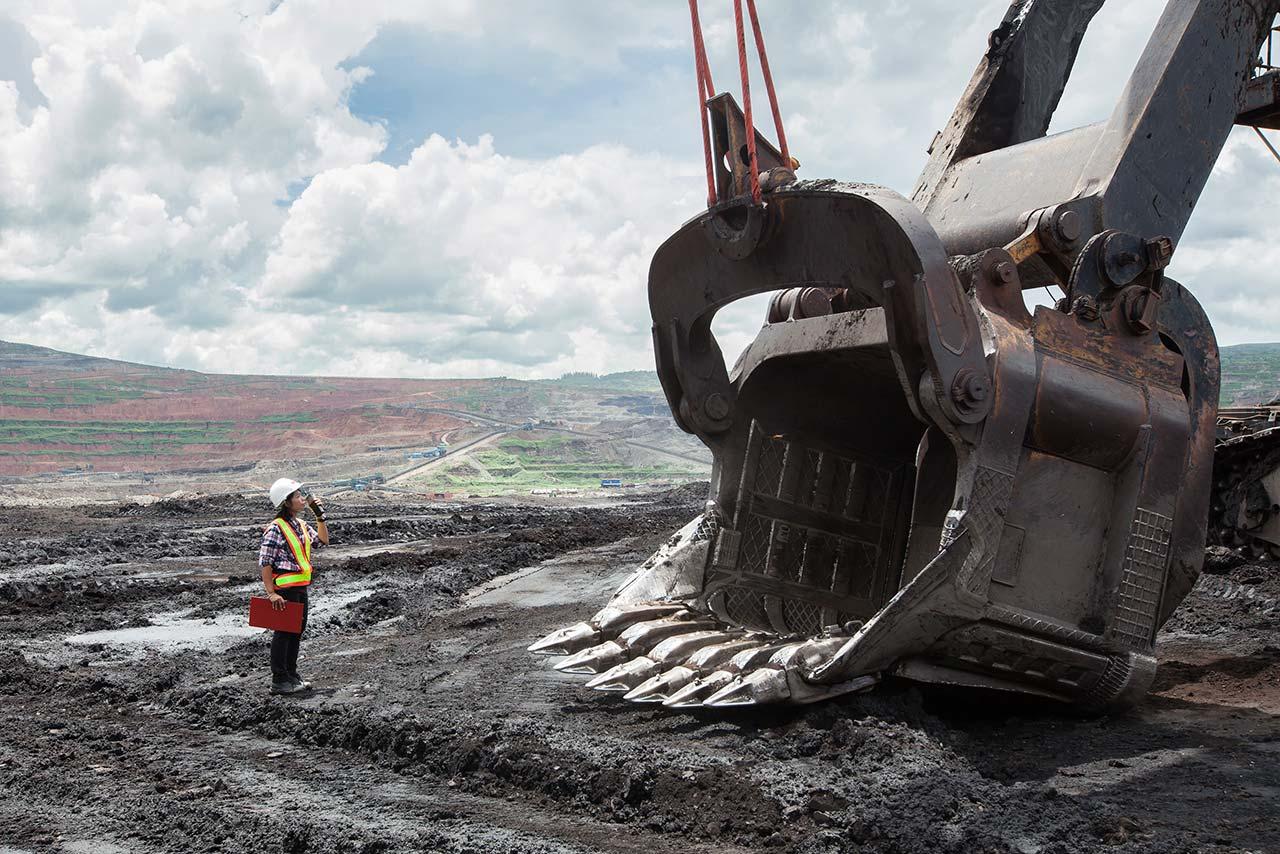
Condition audits
Kuntokartoituksessa käydään kuljettimen rakenne läpi halutussa laajuudessa. Täydellisimmillään aloitetaan kuljettimen teknisistä tiedoista ja verrataan koneistojen, hihnan, rumpujen ja rullien sekä rungon mitoitusta todellisuuden kanssa.
Silmämääräisen tarkastuksen lisäksi on tärkeää keskustella käyttö- ja kunnossapitohenkilöstön kanssa laitteen toiminnasta, jotta myös harvemmin esiintyvistä ongelmatilanteista saadaan käsitys.
Kartoituksen tarkoituksena on tuoda ehdotuksia kuinka hihnakuljettimen huoltovälejä voidaan kasvattaa, huoltoa nopeuttaa ja toiminnan luotettavuutta nostaa. Siis käytännössä tehostaa tuotantoa.
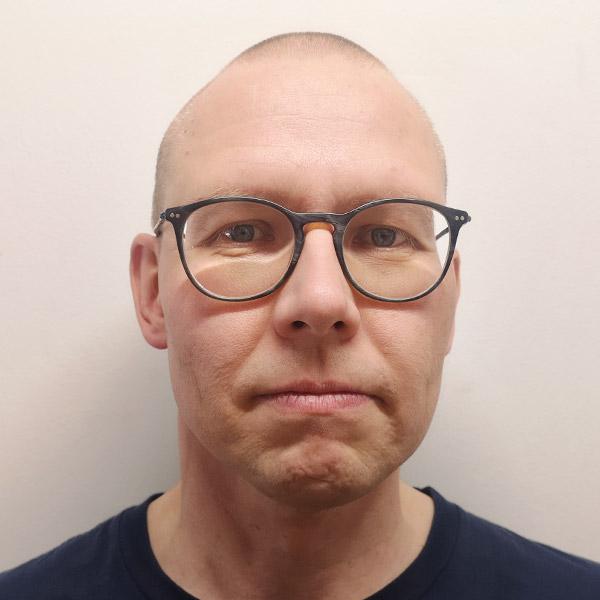
Contact Us
Get in touch with the product manager Petteri Viinanen (040 585 5485, info@sysi.fi) and we’ll tailor a solution to your need.